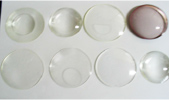
One of the most known disadvantages of plastics is that they are not scratch resistant enough; as a result their optical properties are being deteriorated very quickly due to surface damage. This problem may be alleviated by coating the plastic surfaces (in the form of sheets, ophthalmic lenses or other shapes) with an abrasion and stain resistant thin films that commonly is known as a ‘hard-coat’.
The hard-coated PC sheets could find potential applications in railway windows, airplanes windows in multistoried buildings and automotives and also in plastic optical instruments and components etc. These coatings can also be made colorful by incorporating metal nanoparticles. The hard-coatings developed on CR-39 grade plastic ophthalmic lenses are optically transparent and spot-free and cannot be scratched with #000 grade steel wools! The hard coatings developed on other plastics (PC, PMMA, PP etc.) have also passed all standard international specifications (ASTM) related to the adhesion (highest quality), abrasion (pencil hardness >4H-6H), chemical durability and thermal tests. These anti scratch coatings can also be applicable for previously tinted plastics. Photograph of hard-coated plastics.
These coatings are based on high and low refractive index (two layer optical design) layers having reflection minima at different wavelengths on plastic lenses and sheets for better viewing purposes. Although plastics are transparent, some amount of light (10% or more) is not entering into our eyes due to surface reflection. The purpose of AR coating is therefore to minimize this unwanted reflection of light. In this development the low and high index layers were designed based on low and high index inorganic-organic hybrid nanocomposite layers. The reflection loss at the desired wavelength can be minimized to about 1%. As the reflection minima (see the photographs) can be tuned at different wavelengths, different reflecting colours are being generated which has also beautiful cosmetic appeal.
A nano-structured super-hydrophobic material that provides easy roll of water from the windshield exteriors during the rain. It provides excellent visibility in wet weather driving. The materials has excellent adhesion with glass substrate an its tough enough to prevents from scratch or any mechanical damages. Hence provides long time durable performance.
The use of chromates is toxic due to carcinogenic nature of chromium (VI). The environmental concerns dictate the elimination of current chromate-based surface treatment technologies and development of fundamentally new chromate-free coating systems that can provide long-term and environmentally benign corrosion protection.
Our sol-gel coating after application on zinc and zinc alloy coated substrate enhanced the corrosion resistance properties of the substrate. The coatings can be applied on galvanized steel as well as mild steel with a coating thickness of max.10µm. In this coating thickness, panel passed more than 1000 hrs in salt spray test and 2000 hrs in cyclic corrosion test. This coating technology is environmental friendly and can very easily substitute carcinogenic chromes causing many health hazards. Apart from the excellent corrosion resistance, these coating have excellent scratch resistance, formability, flexibility, solvent, acid and alkali resistance. The sol-gel coating decreased the surface roughness and coefficient of friction where as enhanced the water repellent properties. These performances are difficult to achieve even using 75-100 µm coating thickness of conventional coatings thereby making this technology economically viable.